
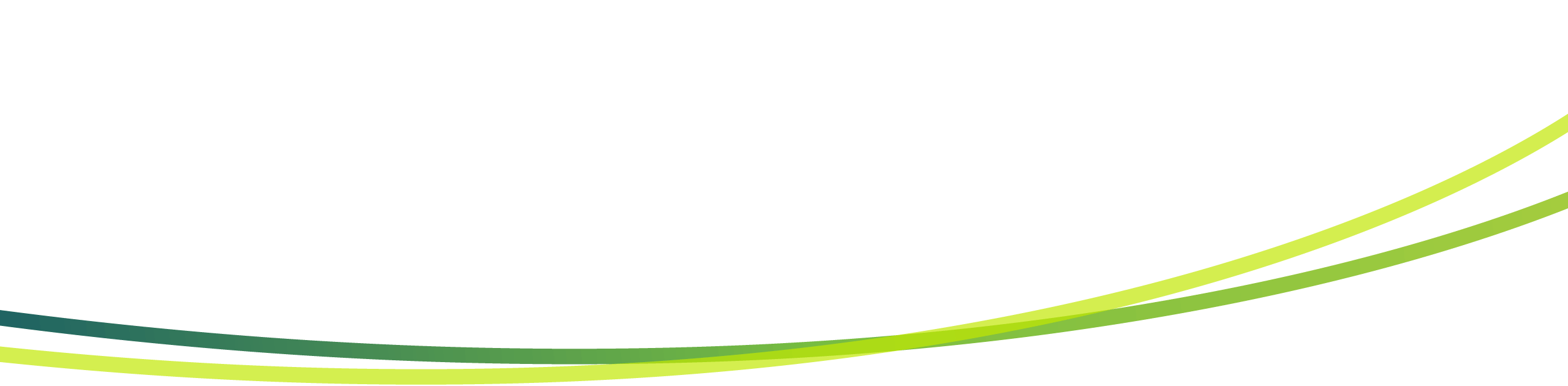
Drug Substance Manufacturing Platforms
As one of the world’s leading CDMOs for vaccines, cell and gene therapeutics, and other biologics, IDT Biologika has a wealth of experience in the biological processes and technologies used to produce Vaccines, Viral Vectors, and Oncolytic Viruses.
Comprehensive Offering
There are virtually no upstream or downstream methods used today that we do not offer. Every process is different, so when process technology is not yet defined by our client, we will evaluate the parameters and define which of several leading technologies we offer will be optimal based on past experience and knowledge.

Cell Factories
IDT Biologika has extensive experience in processes utilizing hyper stack cell factories, which are well established, well-characterized incubation vessels. We offer flexibility in dimensions from a single level up to 40 levels. Our techniques working with cell factories are well characterized and processes are validated through aseptic process simulations (APS). Clients will often bring an existing process using a cell factory, but the process scale may be limited – CF10 for example – so we will scale the process to commercial volume and may transfer it to CF40 to enlarge the batch size.
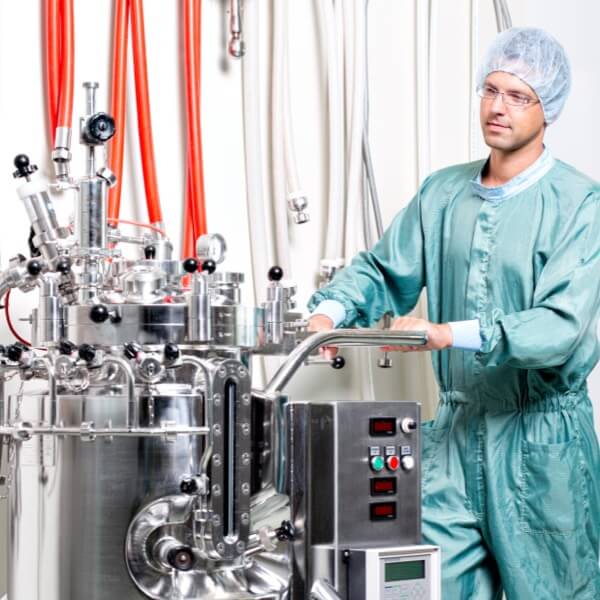
Single-Use Stirred Tank Bioreactors
Single use stirred tank reactors (STRs) are another well-established incubation vessel for cell culturing in live virus manufacturing. At IDT Biologika, the STR technology can be used for both suspension culture and adherent culture. For adherent cell culture, Microcarrier Technology is utilized to provide a very large surface area for the attachment and growth of cells. Adherent cells require a large surface area, and this approach provides an environment for efficient virus harvest.
The larger the surface area, the more cells can be incubated, so space-time yields tend to be higher than cell factories. Other benefits include minimal operator intervention and elimination of some cleaning, sterilization, and validation requirements, mitigating the risk of contamination and optimizing purity. Single-use STRs also reduce mixing times and can optimize the processing time overall, so they are a key technology in viral vaccines and vectors.
As referenced above, IDT Biologika uses microcarrier technology in conjunction with stirred tank bioreactors in cell culturing. The cells grow on surfaces and in the case of microcarriers, they are small particles that contain a certain number of cells where the virus can grow. The microcarrier structures create a very large surface area, so they optimize the number of cells that can grow in the reactor and consequently the amount of virus that is produced.
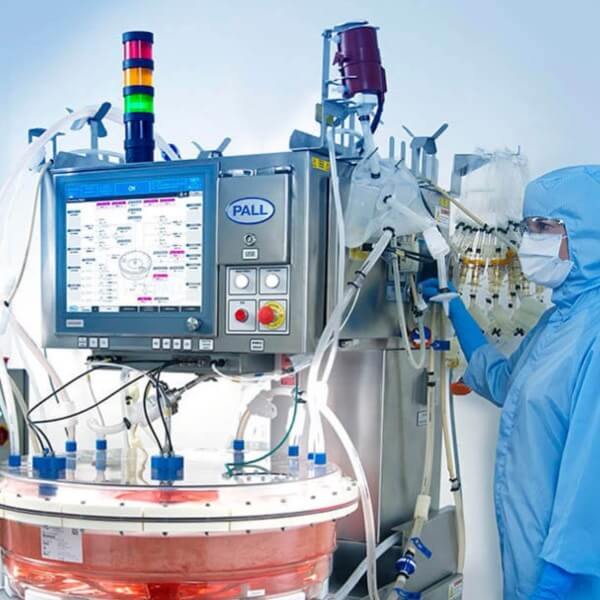
Courtesy of Pall GmbH
iCELLis® – Bioreactor
iCELLis® systems were designed for adherent cell culture applications such as viral vaccine and gene therapy vector production, with the specific goal of simplification and scalability. 2D systems such as cell factories and roller bottles or microcarriers in stirred tank reactors can require a lot of preparation of equipment and manipulation. With iCELLis® bioreactors, you have a fixed batch where cells attach, which is a porous material, and it creates a high surface area to optimize the yield. The cells grow in a 3D environment and there is excellent temperature, pH, and dissolved oxygen control. iCELLis® technology is flexible from small scale to commercial volume, supporting easier process scale-up.
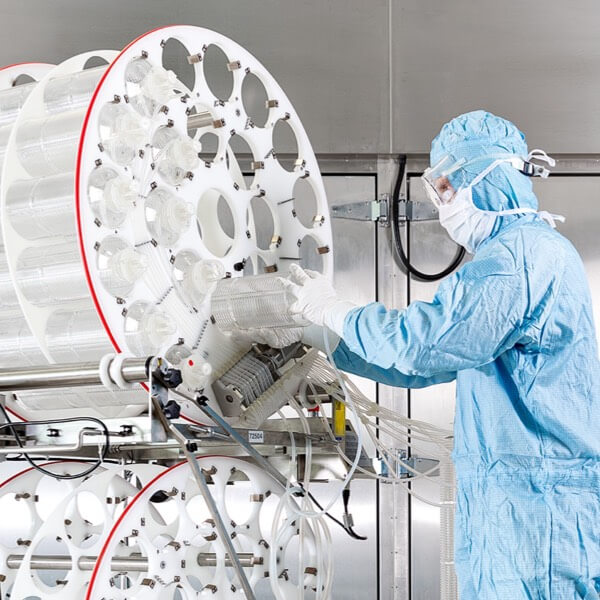
Roller Bottle Technology
Roller bottle systems are a simple incubation system used in cell culture for the manufacture of viral products. It is a 2D system that is used for the cultivation of adherent cells as it provides a very similar process to traditional culture flasks. We can manipulate a limited number of roller bottles with operators, however when a batch size increases to 800 bottles, to maintain sterility, IDT Biologika utilizes a robotic system. This approach supports an aseptic process and ensures it stays free of contamination.